Organic fertilizer production line requires organic fertilizer dryer to improve granulation efficiency
2024/01/09
After the completion of the production and processing of organic fertilizer, it is necessary to consider the storage problem of fertilizer, how to make the fertilizer effect non-volatile, and the important process is actually a part of the processing process of the organic fertilizer production line, that is, the drying of organic fertilizer. After the organic fertilizer dryer dried organic fertilizer particles or powder, the water in which is evaporated in large quantities, and the dried particles can be stored in the warehouse for a long time. The role of organic fertilizer dryer is not only this place, drying is more to test the pelletizing results of organic fertilizer granulator. Good fertilizer particles enter the drying procedure after granulation, and the particles are full and round after drying, but they will not dry and break. If the fertilizer particles after drying have too much cracking and crushing phenomenon, it is necessary to adjust the fertilizer proportion in the previous fermentation and granulation process. Organic fertilizer dryer plays an important role in the fertilizer production process, which is composed of cylinder, gear, pinion, stop roller, drag roller, front roller ring, back roller ring, discharge part, lift plate, reducer, motor, hot air passage, feed chute, furnace body and other parts. When the production capacity is large, multiple hot blast stoves can be equipped, which is simple and good to operate, and the production effect is also good.
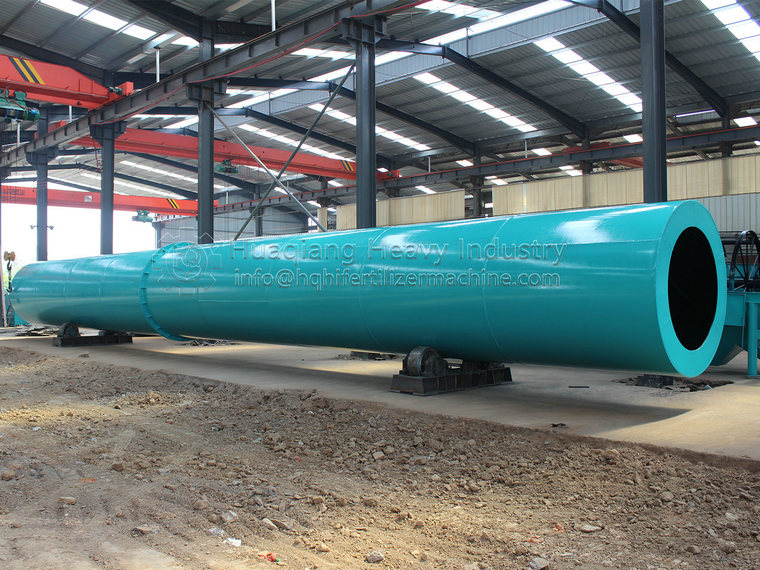
A section of secondary granulation area is set at the front of the organic fertilizer dryer, in which the materials can realize secondary granulation. Then the materials are lifted up through the lifting plate and fully dried. The wet hot air is extracted from the tail of the dryer through the exhaust fan through the pipeline and enters the sedimentation chamber for sedimentation. The tail gas is sprayed to reduce dust through the washing tower after sedimentation. The spray water is pumped out by the water pump for recycling. After secondary dust reduction treatment, the tail gas is discharged into the atmosphere through the chimney.
The dried materials are sent to the cooler through the belt conveyor for cooling. In the cooling process, the natural air is sent to the cooler through the pipeline by the fan to cool the materials. The wind direction in the cooler is countercurrent. The tail gas pumped into the sedimentation chamber through the fan and pipeline is treated as the drying tail gas and discharged into the atmosphere.